相关内容
-
氧化锆增韧氧化铝陶瓷(ZTA)及其应用
氧化铝陶瓷因其优良的力学性能、电性能、化学稳定性,是目前应用广泛的一种陶瓷材料。但是其具有脆性较大、断裂韧性较差的特点,断裂韧性一般为2.5~4.5MPa·m1/2,严重限制了其在更广泛领域的应用,由此,提升氧化铝陶瓷的断裂韧性成为行业内的研究重点之一。而氧化锆增韧氧化铝(zirconia toughened alumina,ZTA)陶瓷结合了氧化铝的高强度和硬度与氧化锆的韧性,成为备受关注的先进陶瓷材料。
-
共晶陶瓷:先进陶瓷中的“一股清流”
近期,工信部国家重点研发计划2024年度项目申报指南发布,共涵盖“高端功能与智能材料、先进结构与复合材料、新型显示与战略性电子材料、高性能制造技术与重大装备、微纳电子技术、新能源汽车”等在内16个重点专项。
-
电子陶瓷的应用前景及发展趋势
电子陶瓷是广泛应用于电子信息领域中的具有独特的电学、光学、磁学等性质的一类新型陶瓷材料,它是光电子工业、微电子及电子工业制备中的基础元件,是国际上竞争激烈的高新技术材料。
行业研究|陶瓷基板的材料与应用
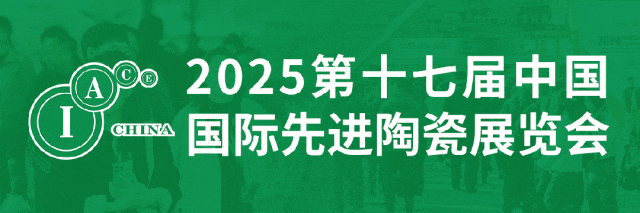
导读:鉴于陶瓷具有良好的导热性、耐热性、高绝缘、高强度、低热胀、耐腐蚀和抗辐射等优点,陶瓷基板在功率器件和高温电子器件封装中得到广泛应用。 其材料主要有Al2O3、AlN、Si3N4、SiC、BeO和BN。由于Al2O3和AlN具有较好的综合性能,两者分别在低端和高端陶瓷基板市场占据主流,而Si3N4基板由于抗弯强度高,在高功率、大温变电力电子器件封装领域发挥重要作用。 |
陶瓷基板的材料
1. 氮化硅:用于机械行业的陶瓷球、半导体功率模块
2. 氧化铝
具有原料来源丰富、价格低廉、绝缘性高、耐热冲击、抗化学腐蚀及机械强度高等优点,综合性能较好,占陶瓷基片材料总量的80%以上。
3. 氮化铝
热导率为氧化铝陶瓷的6~8倍,但热膨胀系数只有其50%,此外还具有绝缘强度高、介电常数低、耐腐蚀性好等优势。除了成本较高外,氮化铝陶瓷综合性能均优于氧化铝陶瓷,是一种非常理想的电子封装基片材料。
4. 氧化铍
BeO材料密度低,热导率高,具有良好的综合性能。
5. 碳化硅、碳化硼
SiC有低热膨胀系数、高热传导率,有优良抗热冲击性,电性能可通过掺杂来实现其绝缘、半导体到导体的转变,是诸多行业的理想材料。但多晶体的SiC热导率低(67W/(m·K)),导电率仅40,是AlN的4倍,限制了其高频应用。
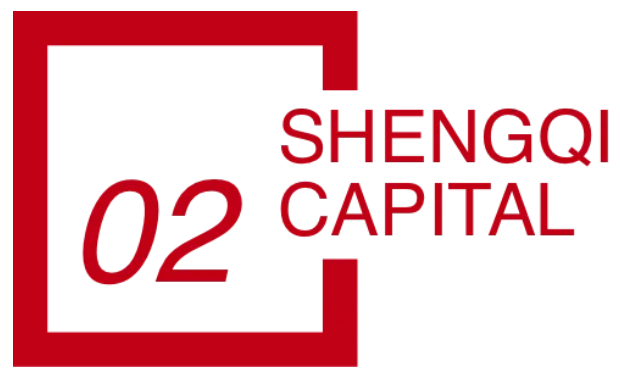
(一)陶瓷基板的分类
1. 平面陶瓷基板
2. 三维陶瓷基板
三维陶瓷基板满足了器件气密封装的需求。主要包括高温/低温共烧陶瓷基板(HTCC/LTCC)、多层烧结三维陶瓷基板(MSC)、直接粘结三维陶瓷基板(DAC)、多层镀铜三维陶瓷基板(MPC)和直接成型三维陶瓷基板(DMC)等。
(二) 平面陶瓷基板的制备技术
1. 薄膜陶瓷基板(TFC)
制备:薄膜陶瓷基板一般采用溅射工艺直接在陶瓷基片表面沉积金属层。 特点:由于溅射镀膜沉积速度低,因此TFC基板表面金属层厚度较小(<1μm),可制备高图形精度(线宽<10μm)陶瓷基板,主要用于激光与光通信领域小电流器件封装。
2. 厚膜印刷陶瓷基板(TPC)
制备:通过丝网印刷将金属浆料涂覆在陶瓷基片上,干燥后经高温烧结(850°C~900°C)制备TPC基板。 特点:TFC基板制备工艺简单,对加工设备和环境要求低,具有生产效率高、制造成本低等优点。由于丝网印刷工艺限制,TFC基板无法获得高精度线路(最小线宽>100μm)。因此TPC仅在对线路精度要求不高的电子器件(如汽车电子)封装中得到应用。
3. 直接键合陶瓷基板(DBC)
制备:首先在铜箔和陶瓷基片间引入氧元素,在1065°C形成Cu/O共晶相,进而与陶瓷基片和铜箔发生反应生成CuAlO2或Cu(AlO2)2,实现铜箔与陶瓷间共晶键合。 特点:由于陶瓷和铜具有良好的导热性,且铜箔与陶瓷间共晶键合强度高,因而具有较高的热稳定性,可满足高温、大电流等极端环境下器件封装应用需求。但DBC在制备过程中要严格控制共晶温度及氧含量,对设备和工艺控制要求较高,生产成本也较高,也无法制备出高精度线路层。
4. 活性金属焊接陶瓷基板(AMB)
制备:AMB基板制备技术是DBC基板工艺的改进:DBC基板制备中铜箔与陶瓷在高温下直接键合,而AMB基板采用活性焊料实现铜箔与陶瓷基片间键合。 特点:由于AMB使用了活性焊料,从而降低陶瓷基板内部热应力,使其结合强度高、可靠性好。该方法成本较高,合适的活性焊料较少,且焊料成分与工艺对焊接质量影响较大,目前只有少数国外企业掌握了AMB基板量产技术。
5. 直接电镀陶瓷基板(DPC)
制备:前端采用了半导体微加工技术(溅射镀膜、光刻、显影等),后端则采用了印刷线路板(PCB)制备技术(图形电镀、填孔、表面研磨、刻蚀、表面处理等),技术优势明显。 特点:DPC基板具有图形精度高,可垂直互连等特性。其优势包括:采用半导体微加工技术,陶瓷基板上金属线路更加精细,适合对准精度要求较高的微电子器件封装;激光打孔与电镀填孔技术实现了陶瓷基板表面垂直互联,实现电子器件三维封装集成,降低器件体积;采用电镀生长控制线路层厚度,并通过研磨降低线路层表面粗糙度,满足高温、大电流器件封装需求;低温制备工艺(<300°C)避免了高温对基片材料和金属线路层的不利影响,同时也降低了生产成本。
6. 激光活化金属陶瓷基板(LAM)
制备:利用特定波长的激光束选择性加热活化陶瓷基片表面,随后通过电镀/化学镀完成线路层制备。 特点:无需光刻、显影、刻蚀等微加工工艺,通过激光直写制备线路层,且线宽由激光光斑决定,精度高;可在三维结构陶瓷表面制备线路层,突破了传统平面陶瓷基板金属化的限制;金属层与陶瓷基片结合强度高,线路层表面平整,粗糙度在纳米级别。虽然LAM技术可在平面陶瓷基板或立体陶瓷结构上加工线路层,但其线路层由激光束“画”出来,难以大批量生产,导致价格极高,目前主要应用在航空航天领域异型陶瓷散热件加工。
(三) 三维陶瓷基板的制备技术
1. 高/低温共烧陶瓷基板(HTCC/LTCC)
制备:HTCC基板制备过程中先将陶瓷粉加入有机黏结剂,混合均匀后成为膏状陶瓷浆料,接着利用刮刀将陶瓷浆料刮成片状,再通过干燥工艺使片状浆料形成生胚;然后根据线路层设计钻导通孔,采用丝网印刷金属浆料进行布线和填孔,最后将各生胚层叠加,置于高温炉(1600°C)中烧结而成。 特点:HTCC基板具有较高机械强度和热导率,物化性能稳定,适合大功率及高温环境下器件封装。但是,HTCC基板制备工艺温度高,制作成本较高,且其线路精度较差,难以满足高精度封装需求。
2. 多层烧结三维陶瓷基板(MSC)
制备:与HTCC/LTCC基板一次成型制备三维陶瓷基板不同,台湾阳升公司采用多次烧结法制备了MSC基板。首先制备厚膜印刷陶瓷基板(TPC),随后通过多次丝网印刷将陶瓷浆料印刷于平面TPC基板上,形成腔体结构,再经高温烧结而成。 特点:MSC基板技术生产设备和工艺简单,平面基板与腔体结构独立烧结成型,且由于腔体结构与平面基板均为无机陶瓷材料,热膨胀系数匹配,制备过程中不会出现脱层、翘曲等现象。其缺点在于:图形精度较低;受丝网印刷工艺限制,MSC基板腔体厚度有限,所以MSC三维基板仅适用于体积较小、精度要求不高的电子器件封装。
3. 直接粘接三维陶瓷基板(DAC)
制备:首先加工金属环和DPC陶瓷基板,然后采用有机粘胶将金属环与DPC基板对准后粘接、加热固化。 特点:由于胶液流动性好,因此涂胶工艺简单,成本低,易于实现批量生产,且所有制备工艺均在低温下进行,不会对DPC基板线路层造成损伤。但是,由于有机粘胶耐热性差,固化体与金属、陶瓷间热膨胀系数差较大,且为非气密性材料,目前DAC陶瓷基板主要应用于线路精度要求较高,但对耐热性、气密性、可靠性等要求较低的电子器件封装。
4. 多层电镀三维陶瓷基板(MPC)
制备:MPC与DPC基板类似,只是在完成平面DPC线路层加工后,再多次光刻、显影和图形电镀完成围坝制备。 特点:MPC以图形电镀工艺制备线路层,避免了HTCC/LTCC与TPC基板线路粗糙问题,满足高精度封装要求;陶瓷基板与金属围坝一体化成型为密封腔体,结构紧凑,无中间粘结层,气密性高;MPC基板整体为全无机材料,具有良好的耐热性,抗腐蚀、抗辐射。其缺点在于:制备过程需要反复进行光刻、显影、图形电镀与表面研磨,耗时长,生产成本高;电镀围坝铜层较厚,内部应力大,基板容易翘曲变形,影响芯片封装质量与效率。
5. 直接成型三维陶瓷基板(DMC)
制备:首先制备平面DPC陶瓷基板,同时制备带孔橡胶模具;将橡胶模具与DPC陶瓷基板对准合模后,向模具腔内填充牺牲模材料;待模材料固化后,取下橡胶模具,将模粘接于DPC陶瓷基板上,并精确复制橡胶模具孔结构特征,作为铝硅酸盐浆料成型模具;随后将铝硅酸盐浆料涂覆于DPC陶瓷基板上并刮平,加热固化,最后将模材料腐蚀,得到含铝硅酸盐免烧陶瓷围坝的三维陶瓷基板。 特点:DMC的出现提高三维陶瓷基板生产效率,同时保证了基板线路精度与可靠性。该工艺制备的三维陶瓷基板精度高,重复性好,适合量产,可满足不同结构和尺寸的电子器件封装要求。
陶瓷基板的应用
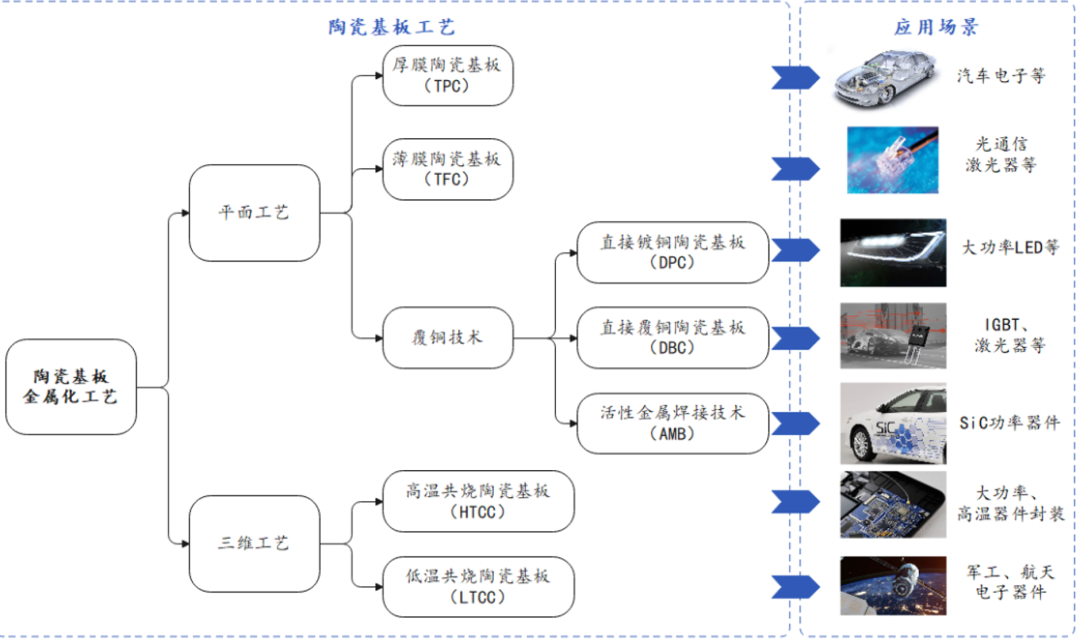
1. 电力电子器件封装
以绝缘栅双极晶体管(IGBT)为代表的第三代电力电子器件具有频率高、功率大和开关速度快等优势,在军工、航天航空、电动牵引、轨道交通、新能源汽车以及家用电子器件领域得到广泛应用。由于IGBT输出功率高,发热量大,散热不良将损坏IGBT芯片。DBC金属线路层较厚,具有载流能力大、耐高温性好及可靠性高等特点,故被广泛使用。
2. 激光器封装
LD广泛应用于工业、军事、医疗和3D打印等领域。由于LD电光转换效率约为50%~60%,工作时大量热量集中在有源区,导致结温升高,因此,在LD封装中必须采用导热性能良好、热膨胀系数匹配的陶瓷基板。由于AlN陶瓷具有热导率高、热膨胀系数低等优点,因此LD封装普遍使用AlN陶瓷基板。
3. 发光二极管(LED)封装
LED是一种基于电光转换的半导体功率器件,具有电光转换效率高、响应快、寿命长和节能环保等优势,目前已广泛应用于通用照明、信号指示、汽车灯具和背光显示等领域。由于陶瓷基板具有高绝缘、高导热和耐热、低膨胀等特性,特别是采用垂直通孔技术的DPC陶瓷基板,可有效满足倒装共晶、COB(板上芯片封装)、CSP(芯片尺寸封装)等技术白光LED封装需求。
4. 热电制冷器(TEC)封装
由于热电制冷效率与半导体粒子数量呈正相关,单位面积粒子数量越多,热电制冷效率越高,DPC陶瓷基板图形精度高,可提高粒子布置密度,从而有效提高热电制冷效率。
5. 高温电子器件(HTE)封装
航空航天、深海钻探、汽车等领域电子器件需要能够在极端环境下工作,因此封装材料必须具有高耐热性和抗湿性,同时器件芯片必须密封于腔体中,避免外界环境的侵蚀和破坏。三维陶瓷基板具有高强度腔体结构,气密性良好,可满足恶劣环境下器件封装要求。
6. 高温器件或其他功率器件封装
聚焦光伏器件封装,由于聚焦作用导致太阳光密度增加,芯片温度升高,必须采用陶瓷基板强化散热。此外,在微波射频领域,为了降低损耗,需采用高频特性良好的HTCC或LTCC基板来提高速度。
陶瓷基板产业链及相关企业
(一) 行业现状
1. 陶瓷基板行业仍为日本主导
日本企业从上世纪已开始在陶瓷领域深耕,目前从陶瓷粉体到陶瓷基板,日本占据全球绝大市场份额。除日本公司外,美国罗杰斯、德国贺利士在陶瓷基板市场中也均占据一席之地,相比之下国内陶瓷基板企业仍存在较大差距。
2. 关键原材料依赖进口
(二) 上游陶瓷粉体
(三) 中游陶瓷基板
陶瓷基板方面,市场份额被日本京瓷、东芝材料,罗杰斯、丸和等海外巨头所占有,我国部分核心零部件的陶瓷基板主要依赖于进口。
从不同金属化工艺来看,日本京瓷在主流陶瓷基板技术应用上占绝对优势,占据全球38.4%的市场份额。其它国外企业如德国贺利士,美国罗杰斯也在全球陶瓷基板领域占据重要位置。国内企业方面,富乐华、同欣电子、陶陶科技等均实现了在主流陶瓷基板技术上的全覆盖。
陶瓷基板的行业壁垒
1. 粉体制备壁垒
2. 陶瓷裸片制备壁垒
(3)气场气流的控制。气动输送流量指空气或物料在气动输送管道中的流动速度。
3. 陶瓷基板制备壁垒
(3)活性钎料的选择和制备。
(二)客户认证壁垒

声 明:文章内容来源于昇祺资本。仅作分享,不代表本号立场,如有侵权,请联系小编删除,谢谢!